One-Piece Flow
Why use it?
One-piece flow (also known as continuous flow or one-work flow) minimizes lead time and inventory. It exposes defects much sooner than batch flow, so that problems can be solved sooner. Because one-piece flow produces only what is needed when it is needed, it also reduces the wastes of transportation, movement, waiting, over-production, over-processing, and defects.
What does it do?
One-piece flow involves producing and moving one item at a time through a series of processing steps as continuously as possible, with each step making just what is needed by the next step. In a continuous flow cell, there is either no piece or one piece between stations. Pieces are not combined into batches. The figure compares batch flow (above) to one-piece flow (below).
Batch Flow vs. One-Piece Flow Diagram
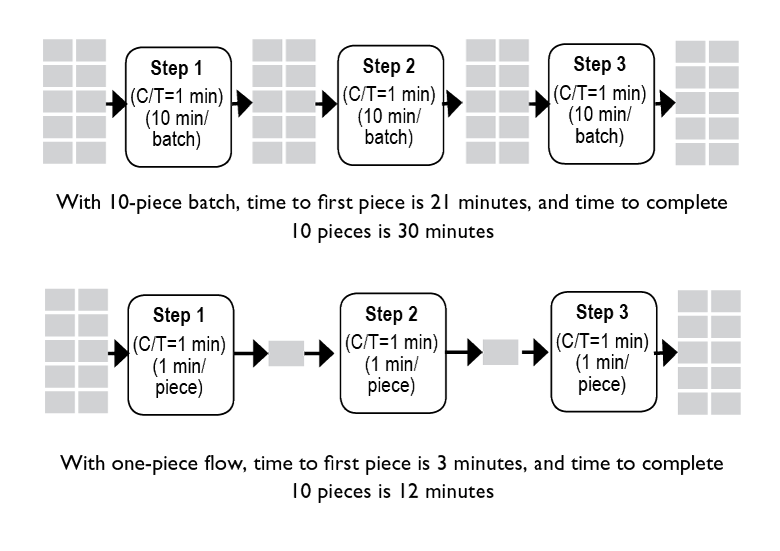
How do I do it?
- Ensure that the changeover time for different products is very short (see Quick Changeover)
- Balance cycle times of each step in the continuous flow process (see Workload Balancing)
- Ensure that the equipment used in each step is reliable (see Total Productive Maintenance)
- Set up a work cell with a cellular layout or straight-line flow (see Work Layout)
- Cross-train all team members
- Pilot the process and make adjustments as necessary
Getting to one-piece flow is a journey that takes time and preparation.
One-piece flow typically enables the use of smaller, less expensive equipment compared to the larger equipment required to handle batches. As older equipment wears out, consider purchasing smaller equipment that is more suited to one-piece flow.